Radartechnik soll bei der Herstellung von Windradflügeln künftig verhindern, dass Produktionsfehler unentdeckt bleiben und Rotorblätter im Betrieb brechen. Die Rechenmodelle dazu sind in Wachtberg programmiert worden.
Programm für RadarWachtberger Technik soll Flügel von Windrädern sicherer machen
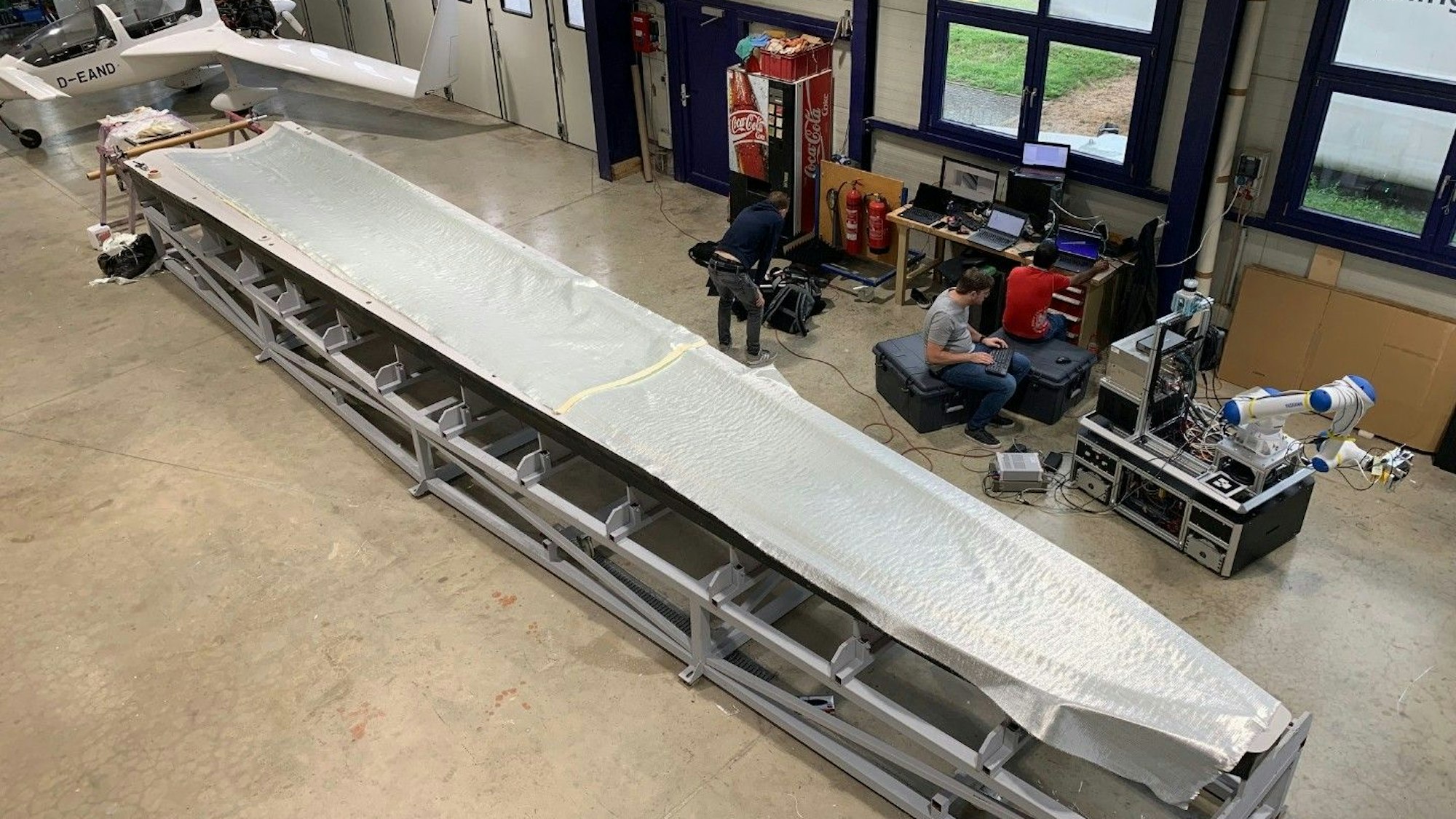
Bei der Aeroconcept GmbH ist für einen Test ein Faserpaket für eine Rotorblattspitze ausgelegt worden
Copyright: Fraunhofer FHR
Zerborstene Flügel an Windrädern geben in jüngster Zeit Rätsel auf: Ohne erkennbare Fremdeinwirkung brachen sie im Betrieb auseinander. Bei Fraunhofer in Wachtberg haben Experten nun ihre Erfahrungen mit Radar in eine neue Technik einfließen lassen, die bereits bei der Herstellung von Rotorblättern im Material Fehler aufspüren kann. Dabei geht es um Faserverbundstoffe aller Art.
Das Fraunhofer-Institut für Hochfrequenzphysik und Radartechnik FHR arbeitet beim Projekt „FiberRadar“ mit der Ruhr-Universität Bochum, der Fachhochschule Aachen und der Aeroconcept GmbH zusammen. Die Technik ist inzwischen so weit gereift, dass sie automatisch während der Herstellung von Rotorblättern in deren Innern nach Fehlern sucht.
Bislang war es nur möglich, nach dem äußeren Erscheinungsbild von Rotorblättern auf Fehler zu schließen. Mit der neuen Technik lassen sich Werkstoffe zerstörungsfrei prüfen. Solche Verfahren gibt es schon in anderen Bereichen. Etwa in der Metallverarbeitung oder bei Lebensmitteln. Aber in solchen Fällen handelt es sich meist um recht homogene Massen. Bei Faserverbundstoffen sind aber Muster in der Struktur normal.
Fehler schon vor der Verbindung mit Kunstharz erkennen
Entsprechend kompliziert ist für Laien die Auswertung der Radarbilder. Kennmuster ergeben letztlich Aufschluss über Fehler im Material. Dazu muss man wissen, dass Faserbundstoffe in der Regel aus Glasfasern bestehen, die verschiedenen geschichtet sein können, also schon gewollt unterschiedliche Faserrichtungen haben können. Meist ist es eine eingefärbte Kunstharzmatrix, die das fertige Produkt zusammenhält und nicht mehr erkennen lässt, wo welche Faser verläuft. Oft sind aber schon so viele Fasern miteinander verwoben, dass schon vor dem Verkleben mit Harz einzelne Fasern nicht mehr mit bloßem Auge kontrolliert werden können.
Bei der Produktion von Rotorblättern werden Glasfaserlagen übereinander in einer Schale ausgelegt. Erfolgt dies nicht akkurat, kann es zu verschiedenen Defekten wie Wellenbildungen beziehungsweise Ondulation kommen.
„Bei der Produktion von Rotorblättern werden Glasfaserlagen übereinander in einer Schale ausgelegt. Erfolgt dies nicht akkurat, kann es zu verschiedenen Defekten wie Wellenbildungen beziehungsweise Ondulation kommen. Aber auch die Richtung der Faser kann sich verdrehen und somit die mechanischen Eigenschaften des Bauteils beeinflussen“, erläutert Projektleiter Dr. André Froehly vom Fraunhofer FHR in Wachtberg. Schlimmstenfalls sieht ein Produkt später genau richtig aus, ohne ausreichend stabil zu sein.
Zwar gab es für Faserverbundstoffe schon technische Prüfverfahren. Sie wurden zum Beispiel mit Ultraschall untersucht. Damit sind laut Froehly aber erst beim fertigen Produkt Fehlstellen zu finden. Eine Kontrolle während der Produktion war nicht möglich, und wenn ein Produkt als fehlerhaft erkannt wurde, blieb meist bloß die Verschrottung möglich.
Radarstrahlen im Millimeterwellenbereich
Mit der Technik aus Wachtberg kann nun aber schon das Zusammenlegen der Fasen im Scan mit Radarstrahlen in Millimeterwellen überwacht werden. Dabei wirken ein Roboter und ein voll-polarimetrischer Radar zusammen. Anders als übliche Radare sendet das Gerät Signale in zwei Polarisationen aus. Auch empfangen wird in zwei Polarisationen. „Damit lassen sich nicht nur Faserstrukturen hochauflösend darstellen, sondern auch Defekte in tieferen Schichten einfach offenlegen“, erklärt Froehly.
Störende Effekte werden weggerechnet, so dass die Forscher das gesamte Material schichtweise kontrollieren können. An der neuen Technik stammen vor allem die Berechnungsmethoden aus Wachtberg. Das aktuelle Projekt ist abgeschlossen. Es wurde aus den Mitteln des Europäischen Fonds für regionale Entwicklung (EFRE) gefördert. Ein Folgeprojekt soll noch die Weiterentwicklung und Produktionsreife beinhalten. Bei der Tiefenauflösung sowie der Erkundungsgeschwindigkeit gibt es offenbar noch Verbesserungsmöglichkeiten, wie Froehly andeutete.